jueves, 26 de junio de 2008
EQUIPOS Y ACCESORIOS
Es cualquier herramienta que identifica el color matiz para una medida más objetiva de color.
Permite la absorbencia de una solución en una específica frecuencia de la luz a ser determinada.
Por eso, que hacen descubrir la concentración de un soluto conocido que sea proporcional a la absorbencia.
EQUIPOS
Colorímetro, colorímetro espectral según DIN 5033.
TECNICA OPERATORIA
Opera según el procedimiento espectral, que está considerado como el método de medición más preciso con una gran diferencia con respecto a otros métodos. Una fuente de luz indefinida ilumina la prueba y la luz reflejada por la superficie la luz se mide de un modo espectral.
Puesto que los colores superficiales dependen de la fuente de iluminación, el espectro reflejado debe ser ponderado con una fuente de luz estandarizada. El espectro resultante es valorado con los tres espectros basados en la percepción en la percepción al rojo, verde, azul del sistema de visión y humano y así se obtienen tres valores cromáticos x, y y z.
Del mismo modo que el caso de las fuentes de luz, las tres funciones de percepción cromática están estandarizadas para un ángulo de observación
INTERPRETACION DE RESULTADOS
Es importante convertir los valores de colores básicos (valores de espectro normales) x, y, z en otros valores de colores para ellos podrá servirse de los múltiples sistemas de color como y, x, y l* a* b* o l* u* v* la diferencia de color E, ósea la diferencia entre dos colores, se calcula de la suma de diferencias de los tres valores cromáticos para un área cromática determinada.
ESPECTROMETRO
La espectrometría de emisión atómica aplicada a los metales es un método más que adecuado para resolver los problemas de composición química de cada aleación. Utilizando esta técnica el operador puede llevar a cabo análisis cuantitativos, semi –cuantitativos y en algunos casos incluso cualitativos, para identificar positivamente la mayoría de elementos en un componente antes de instalación a un sistema.
TECNICA OPERATORIA
Es la observación de espectros de emisión atómica de diversos metales. El sistema de esta medida no es destructivo y no requiere preparación de muestra pudiéndose realizar la medida “in situ”. El principio en que se basa el espectrómetro es la generación de un arco entre un electrodo metálico y al pieza de trabajo (a analizar). La energía del arco es suficiente para vaporizar una pequeña porción del metal y causar la ionización de los átomos de muestra mediante (la excitación de electrodos) produciendo por tanto emisiones de luz que se procesaran mediante la óptica del instrumento.
INTERPRETACION DE RESULTADOS
Tiene el mismo fundamento que la fotografía de emisión de llama, se trata de conocer si una sustancia está presente en la muestra y qué cantidad. Medimos landa de la REM emitida de la U la I de la radiación emitida. La I será % al número de átomos excitados.
Película fotográfica, tubos multiplicadores. La espectrometría significa análisis cuantitativo, para ello debemos el espectrómetro de emisión del elemento, cuantas líneas se pueden detectar mayor será la exactitud y conocer landa de las líneas espectrales en una película a la landa en la que se produce transición aparecerá una banda luminosa.
ELECTROLISIS
Es una manera de producir cambios químicos a través de reacciones de electrodos en contacto con el electrolito por el paso d una corriente eléctrica las celdas de electrolisis generalmente consta de electrodos conectados a una fuente externa de electricidad (un suministro de de fuerza o bacteria) y sumergido en un liquido que puede conducir electricidad a través del movimiento de iones.
TECNICA OPERATORIA
Para que tenga lugar la electrolisis de un compuesto es preciso que este sea un acido o una sal disociable en iones, que se hallen en estado liquido o en disolución. Dicho compuesto llamado electrolisis, se coloca en un recipiente (cuba electrolítica) en el que existen dos electrodos en los que se establecen una diferencia potencial bajo el flujo de la cual los iones positivos (cationes) son atraídos hacia el cátodo (negativo) donde adquieren el o los electrones que precisan para convertirse en átomos del elemento mientras que los iones negativos (aniones ) se dirigen hacia el ánodo (positivo) donde ceden sus electrones sobrantes para alcanzar la estructura atómica estable.
INTERPRETACION DE RESULTADOS
Flujo de corriente medido en amperios (donde 1Aes igual pasaje de columbio de carga por segundo) representa la velocidad de flujo de carga eléctrica a través de la celda de electrolisis. La cantidad de una sustancia producida o agotada en la reacción en un electrodo es proporcional a la cantidad de electricidad (culombios) pasando durante electrolisis (F una corriente constante de 1 A pasando para 1h equivalente a 3600 culombios) producirá 0.018656 mol o 13228g de cloro. La cantidad de electricidad es la integral de la corriente sobre la duración de la electrolisis y puede estar determinada con un culombímetro.
miércoles, 25 de junio de 2008
NO FERROSOS
COBRE
El cobre, de símbolo Cu, es el elemento químico de número atómico 29. Se trata de un metal de transición de color rojizo y brillo metálico que, junto con la plata y el oro, forma parte de la llamada familia del cobre, caracterizada por ser los mejores conductores de electricidad. Gracias a su alta conductividad eléctrica, ductilidad y maleabilidad, se ha convertido en el material más utilizado para fabricar cables eléctricos y otros componentes eléctricos y electrónicos.El cobre forma parte de una cantidad muy elevada de aleaciones que generalmente presentan mejores propiedades mecánicas, aunque tienen una conductividad eléctrica menor. Las más importantes son conocidas con el nombre de bronces y latones. Por otra parte, el cobre es un metal duradero porque se puede reciclar un número casi ilimitado de veces sin que pierda sus propiedades mecánicas.
- Caracteristicas:
Propiedades físicas:El cobre posee varias propiedades físicas que propician su uso industrial en múltiples aplicaciones, siendo el tercer metal, después del hierro y del aluminio, más consumido en el mundo. Es de color rojizo y de brillo metálico y, después de la plata, es el elemento con mayor conductividad eléctrica y térmica. Es un material abundante en la naturaleza; tiene un precio asequible y se recicla de forma indefinida; forma aleaciones para mejorar las prestaciones mecánicas y es resistente a la corrosión y oxidación. La conductividad del cobre recocido medida a 20 ºC es igual a 58,1086 S/m. Su punto de fusion es de 1083.
- Aleaciones:
Laton:
El latón, también conocido como cuzin, es una aleación de cobre, zinc (Zn) y, en menor proporción, otros metales. Se obtiene mediante la fusión de sus componentes en un crisol. En los latones industriales, el porcentaje de Zn se mantiene siempre inferior a 50%. Su composición influye en las características mecánicas, la fusibilidad y la capacidad de conformación por fundición, forja y mecanizado. En frío, los lingotes obtenidos se deforman plásticamente produciendo láminas, varillas o se cortan en tiras susceptibles de estirarse para fabricar alambres. Su densidad depende de su composición y generalmente ronda entre 8,4 g/cm3 y 8,7 g/cm3.Las características de los latones dependen de la proporción de elementos que intervengan en la aleación de tal forma que algunos tipos de latón son maleables únicamente en frío, otros exclusivamente en caliente, y algunos no lo son a ninguna temperatura. Todos los tipos de latones se vuelven quebradizos cuando se calientan a una temperatura próxima al punto de fusión.El latón es más duro que el cobre, pero fácil de mecanizar, grabar y fundir. Es resistente a la oxidación, a las condiciones salinas y es maleable, por lo que Puede laminarse en planchas finas. Su maleabilidad varía la temperatura y con la presencia, incluso en cantidades mínimas, de otros metales en su composición.
Bronce:
Las aleaciones en cuya composición predominan el cobre y el estaño (Sn) se conocen con el nombre de bronce. Hay muchos tipos de bronces que contienen además otros elementos como aluminio, berilio, cromo o silicio. El porcentaje de estaño en estas aleaciones está comprendido entre el 2 y el 22%. Son de color amarillento y las piezas fundidas de bronce son de mejor calidad que las de latón, pero son más difíciles de mecanizar y más caras. El bronce se emplea especialmente en aleaciones conductoras del calor, en baterías eléctricas y en la fabricación de válvulas, tuberías y uniones de fontanería. Algunas aleaciones de bronce se usan en uniones deslizantes, como cojinetes y descansos, discos de fricción; y otras aplicaciones donde se requiere alta resistencia a la corrosión como rodetes de turbinas o válvulas de bombas, entre otros elementos de máquinas. En algunas aplicaciones eléctricas es utilizado en resortes. Su punto de fusion es de
ALUMINIO
El aluminio es un elemento químico, de símbolo Al y número atómico 13. Se trata de un metal no ferroso. Es el tercer elemento más común encontrado en la corteza terrestre. Los compuestos de aluminio forman el 8% de la corteza de la tierra y se encuentran presentes en la mayoría de las rocas, de la vegetación y de los animales. En estado natural se encuentra en muchos silicatos (feldespatos, plagioclasas y micas). Como metal se extrae del mineral conocido con el nombre de bauxita, por transformación primero en alúmina mediante el proceso Bayer y a continuación en aluminio mediante electrólisis.Este metal posee una combinación de propiedades que lo hacen muy útil en ingeniería mecánica, tales como su baja densidad (2.700 kg/m3) y su alta resistencia a la corrosión. Mediante aleaciones adecuadas se puede aumentar sensiblemente su resistencia mecánica (hasta los 690 MPa). Es buen conductor de la electricidad, se mecaniza con facilidad y es relativamente barato. Por todo ello es el metal que más se utiliza después del acero.
Caracteristicas:
Características físicas:Entre las características físicas del aluminio, destacan las siguientes:-Es un metal ligero, cuya densidad o peso específico es de 2700 kg/m3 (2,7 veces la densidad del agua).
-Tiene un punto de fusión bajo: 660ºC (933 K).-El peso atómico del aluminio es de 26,9815.-Es de color blanco brillante.
-Buen conductor del calor y de la electricidad.
-Resistente a la corrosión, gracias a la capa de Al2O3 formada.
-Abundante en la naturaleza.
-Material fácil y barato de reciclar.
ESTAÑO:
Es un metal plateado, maleable, que no se oxida fácilmente con el aire y es resistente a la corrosión. Se encuentra en muchas aleaciones y se usa para recubrir otros metales protegiéndolos de la corrosión. Una de sus características más llamativas es que bajo determinadas condiciones forma la peste del estaño. Al doblar una barra de este metal se produce un sonido característico llamado grito del estaño, producido por la fricción de los cristales que la componen.
El estaño puro tiene dos variantes alotrópicas: El estaño gris, polvo no metálico, semiconductor, de estructura cúbica y estable a temperaturas inferiores a 13,2 ºC, que es muy frágil y tiene un peso específico más bajo que el blanco. El estaño blanco, el normal, metálico, conductor, de estructura tetragonal y estable a temperaturas por encima de 13,2 ºC.
Aplicaciones
Se usa como revestimiento protector del cobre, del hierro y de diversos metales usados en la fabricación de latas de conserva.
Su uso también es de disminuir la fragilidad del vidrio.
Los compuestos de estaño se usan para fungicidas, tintes, dentifrícos (SnF2) y pigmentos.
Se usa para hacer bronce, aleación de estaño y cobre.
Se usa para la soldadura blanda.
En etiquetas Es un metal plateado, maleable, que no se oxida fácilmente con el aire y es resistente a la corrosión. Se encuentra en muchas aleaciones y se usa para recubrir otros metales protegiéndolos de la corrosión. Una de sus características más llamativas es que bajo determinadas condiciones forma la peste del estaño. Al doblar una barra de este metal se produce un sonido característico llamado grito del estaño, producido por la fricción de los cristales que la componen.
El estaño puro tiene dos variantes alotrópicas: El estaño gris, polvo no metálico, semiconductor, de estructura cúbica y estable a temperaturas inferiores a 13,2 ºC, que es muy frágil y tiene un peso específico más bajo que el blanco. El estaño blanco, el normal, metálico, conductor, de estructura tetragonal y estable a temperaturas por encima de 13,2 ºC.
METALES FERROSOS
FUNDICION GRIS:
Son aleaciones hipoeutecticas que contienen entre 2,5 y 4% de Carbono, funde entre los 1200-1300ºC, su aspecto en la superficie exterior es de color gris oscuro y su peso especifico puede ser de 7-7,2. El proceso de grafitizacion se realiza con mayor facilidad si el contenido de carbono es elevado, las temperaturas elevadas y si la cantidad de elementos grafitizantes presentes, especialmente el silicio, es la adecuada, ademas de controlar la velocidad de enfriamiento para obtener una estructura perlitica o ferritica y en ella laminas de grafito que se clasifican segun so forma distribucion y tamaño.La fundicion gris es muy mecanizable en todo tipo de maquinas de herramientas excepto en rectificadoras, admiten bien el taladrado, el roscado y son soldables. Segun su composicion la fundicion gris posee mayor fluidez llenando bien los moldes.* Propiedades:Resistencia a la tracción: la fundiciíon gris tiene una carga de rotura a la tracción pequeña, entorno a los 15 kg/mm² y llega a los 30 , 40 y 45 kg/ mm² según sea su composición.Resistencia a la comprensión: esta resistencia es mayor, y para las fundiciones grises normales resulta cerca de tres veces la de la tracción, por eso, sus aplicaciones principales se da en piezas sometidas a esfuerzos de compresión, más bien que a los de tracción. Resistencia a la flexión: puesto que en la flexión las fibras del elemento quedan tensas en la parte convexa, y comprimidas en la cóncava, la resistencia a la flexión varia según la orientacion de la sección. Resistencia al choque: el choque y la resiliencia son solicitaciones dinámicas, y en su confrontación la fundición se comporta de un modo particular. Las fundiciones grises , resisten muy mal los choques y son frágiles porque no sufren deformaciones plásticas.
Dureza: la dureza de la fundición gris es relativamente elevada, esta varía entre 130 a 300 Brinell según sea su composición. A pesar de su elevada dureza se puede mecanizar fácilmente, porque la viruta se desprende mejor y por la presencia de grafito liberado, que lubrica el paso de la viruta sobre el corte de la herramienta.
Resistencia química: la fundición tiene poca resistencia química, y se deteriora con los ácidos, los álcalis y las oxidaciones. Otras propiedades: la fundición gris no es dúctil, no es maleable; se puede soldar al latón; en la soldadura oxiacetilénica y en la eléctrica de arco. La fundición puede recibir baños galvánicos (ser niquelada, por ejemplo), ser galvanizada en caliente, estañada y esmaltada al fuego (piezas de uso doméstico y para la industria química).
- FUNDICION NODULAR: Metal que funde a 1100ºC, su peso especifico esta entre 7,3-7,4,la mayor parte del contenido de carbono en el hierro nodular, tiene forma de esferoides. Para producir la estructura nodular el hierro fundido que sale del horno se inocula con una pequeña cantidad de materiales como magnesio, cerio, silicio y cromo, los cuales se adicionan al caldero antes de colar el metal en los moldes, la cantidad de ferrita presente en la matriz depende de la composición y de la velocidad de enfriamiento. Este tipo de fundición se caracteriza por que en ella el grafito aparece en forma de nodulos y así la continuidad de la matriz se interrumpe mucho menos que cuando se encuentra en forma laminar, esto da lugar a una resistencia a la tracción y tenacidad mayores que en la fundición gris ordinaria.
* Propiedades:La fundicion nodular presenta en ciertos casos propiedades comparables con las de los aceros, por ejemplo el modulo de elasticidad, que puede alcanzar valores de hasta 17500 Kg/mm2 cuando se encuentra en estado recocido; presentan, además, valores de resiliencia y porcentaje de elongación muy por encima de las fundiciones pero por debajo de los aceros. Los valores de límite de elasticidad varían entre un 65 y un 85% de la última carga de acuerdo al tratamiento que se le realice a la fundición después de la inoculación. Cuando la fundición es empleada en estado bruto de colada presenta una resistencia a la tracción de aproximadamente unos 70 Kg/mm2 y un 3% de alargamiento. Cuando se desea una relativamente buena dureza y una aceptable ductilidad se recomienda utilizar fundiciones esferoidales que hayan sido sometidas a normalizado y revenido o bien a temple y revenido ya que se pueden obtener por medio de estos tratamientos resistencias a la tracción que varían entre 80 y 90 Kg/mm2 y porcentajes de alargamiento entre 1.5 y 2.0%.
FUNDICION BLANCA:
La fundicion blanca contiene de 2,5 a 3% de carbono, funde entre los 1100º y 1200ºC, es menos fluida que la gris, se contrae algo al solidificarse y el carbono se presenta en forma de carburo de hierro (cementita). Es muy dura, carece de maleabilidad, es fragil y de estructura fibrosa de grano chico; la superficie de fractura es de color blanco, el peso especifico es de 7,4-7,6,. La formacion del grafito combinado o cementita se da por un bajo porcentaje de C y Si, ademas de una rapida velocidad de enfriamiento. Estas fundiciones se caracterizan por su dureza y resistencia al desgaste, siendo sumamente quebradiza y difícil de mecanizar. Esta fragilidad y falta de maquinabilidad limita la utilización industrial de las fundiciones " totalmente blancas ", quedando reducido su empleo a aquellos casos en que no se quiera ductilidad como en las camisas interiores de las hormigoneras, molinos de bolas, algunos tipos de estampas de estirar y en las boquillas de extrusión.Se clasifican en:- fundicion blanca perlitica: Tiene una resistencia a la traccion de 21kg/mm2, una tenacidad de 1,27-1,87 kgf y una dureza: 500-600 Brinell.- fundicion blanca martensitica: Tiene una resistencia a la traccion de 35-42 kg/mm2, tenacidad:1,60-1,72 kgf y una dureza: 600 Brinell
ACERO ESTRUCTURAL
- Descripcion: Es fundamentalmente una aleación de hierro (mínimo 98 %), con contenidos de carbono menores del 1 % y otras pequeñas cantidades de minerales como manganeso, para mejorar su resistencia, y fósforo, azufre, sílice y vanadio para mejorar su soldabilidad y resistencia a la intemperie. Es un material usado para la construcción de estructuras, de gran resistencia, producido a partir de materiales muy abundantes en la naturaleza. Entre sus ventajas está la gran resistencia a tensión y compresión y el costo razonable.A pesar de la susceptibilidad al fuego y a la intemperie es el material estructural más usado, por su abundancia, facilidad de ensamblaje y costo razonable.
- Propiedades:Alta resistencia: la alta resistencia del acero por unidad de peso, permite estructuras relativamente livianas, lo cual es de gran importancia en la construcción de puentes, edificios altos y estructuras cimentadas en suelos blandos.
Homogeneidad: las propiedades del acero no se alteran con el tiempo, ni varían con la localización en los elementos estructurales.
Elasticidad: el acero es el material que más se acerca a un comportamiento linealmente elástico, hasta alcanzar esfuerzos considerables.Precisión dimensional: los perfiles laminados están fabricados bajo estándares que permiten establecer de manera muy precisa las propiedades geométricas de la sección.Ductilidad: el acero permite soportar grandes deformaciones sin falla, alcanzando altos esfuerzos en tensión, ayudando a que las fallas sean evidentes.
Tenacidad: el acero tiene la capacidad de absorber grandes cantidades de energía en deformación (elástica e inelástica).Facilidad de unión con otros miembros: el acero en perfiles se puede conectar fácilmente a través de remaches, tornillos o soldadura con otros perfiles.Rapidez de montaje: la velocidad de construcción en acero es muy superior al resto de los materiales.Disponibilidad de secciones y tamaños: el acero se encuentra disponible en perfiles para optimizar su uso en gran cantidad de tamaños y formas.Costo de recuperación: las estructuras de acero de desecho, tienen un costo de recuperación en el peor de los casos como chatarra de acero.
Reciclable: el acero es un material 100 % reciclable además de ser degradable por lo que no contamina.Permite ampliaciones fácilmente: el acero permite modificaciones y/o ampliaciones en proyectos de manera relativamente sencilla.Corrosión: el acero expuesto a intemperie sufre corrosión por lo que deben recubrirse siempre con esmaltes alquidálicos (primarios anticorrosivos) exceptuando a los aceros especiales como el inoxidable.
- Clasificacion:
Planchas: Es un producto plano de acero laminado en caliente con anchos de 203 milímetros y 1219 milímetros, y espesores mayores de 5,8 milímetros y mayores de 4,5 milímetros, respectivamenteNormas técnicas ASTM A-569, A-36, A-283 grado C. Descripción y uso Planchas de acero laminadas en caliente, destinadas a la construcción de silos, embarcaciones pesqueras, vagones, estructuras y otros usos en general.
ACERO PARA HERRAMIENTAS
En este grupo se incluyen todos los aceros que normalmente se emplean para la fabricación de útiles o herramientas destinados a modificar la forma, tamaño y dimensiones de los materiales por cortadura, por presión o por arranque de viruta.Los aceros de herramientas tienen generalmente un contenido en carbono superior a 0.30%, aunque a veces también se usan para la fabricación de ciertas herramientas, aceros de bajo contenido en carbono (0.1 a 0.30%).-
Propiedades:
Penetración del temple:La mayor o menor penetración del temple es función de la templabilidad de cada clase de acero en particular. La clasificación dada en función de la templabilidad está establecida en el supuesto de que se utilicen los medios de temple recomendados. Los aceros de temple superficial, entre los que se encuentran los aceros de herramientas al carbono, los aceros al tungsteno, se templan por lo general en agua. La templabilidad de los aceros aumenta con el contenido en elementos de aleación, excepto en el caso del cobalto, el cual es único elemento que la hace disminuir. Para que en una sección grande la tenacidad tenga en toda ella un valor elevado, conviene elegir un acero de alta aleación.Tenacidad:En el caso de los aceros de herramientas, el término tenacidad se refiere más a la capacidad de sufrir golpes sin rotura que a la facultad de absorber energía durante la deformación. La mayor parte de las herramientas tienen que ser piezas rígidas, y por lo general cualquier deformación que presenten, por pequeña que sea, las hace inservibles. Los aceros de herramientas con contenidos en carbono medios y bajos, son los que presentan mejor tenacidad y constituyen el material utilizado en la fabricación de herramientas resistentes al choque.Dureza en caliente:Esta propiedad expresa la resistencia que presenta el acero al ablandamiento a temperaturas elevadas, y viene reflejada, en cierto modo, por la resistencia que ofrece el material al revenido, la cual constituye un factor importante a considerar en la elección de los aceros de herramientas que trabajen a más de 500ºC es fundamental que posean aleación
.Maquinabilidad:Esta propiedad indica la mayor o menor facilidad que presenta el material a su mecanización y a la obtención de un acabado perfecto. Los factores que influyen en la maquinabilidad de los aceros de herramientas son la dureza en estado de recocido, la micro estructura del acero y la cantidad de carburos presentes.En comparación con los aceros aleados normales, los aceros de herramientas son mucho más difíciles de mecanizar. El acero de herramienta que presenta mejor maquinabilidad tiene un índice aproximadamente igual al 30%, por lo tanto como referencia para comparar la maquinabilidad de los distintos aceros de herramientas. La maquinabilidad y facilidad de trabajo de los aceros de herramientas disminuye al aumentar el contenido de carbón y elementos de aleados. Conforme aumenta el contenido en carbono y elementos de aleación en los aceros, carbono en combinación con elementos que tienen gran tendencia a formar carburos, como el vanadio, el tungsteno, el cromo y el molibdeno, reduce la maquinabilidad al formarse gran número de partículas duras de carburo, que no se disuelven en el recocido.Resistencia a la descarburación:Ya que ésta determina la instalación a utilizar en el tratamiento térmico, y la cantidad de material que es necesario quitar de la superficie después del temple. La descarburación tiene lugar normalmente cuando los aceros se calientan a temperaturas superiores a 704ºC t salvo que el material se proteja en el calentamiento por algún procedimiento, como, por ejemplo, mediante la utilización de una atmósfera protectora, es probable que la superficie del acero pierda algo de carbono. Esta descarburación es la causa de que en el temple la superficie no se endurezca, sino que quede blanda.Los aceros de herramientas al carbono son los que menos se descarburan. Los aceros para la fabricación de herramientas para trabajos de choque presentan una resistencia a la descarburación baja; los utilizados en las herramientas para trabajos en caliente se consideran que tienen una resistencia mediana, y la mayoría de los restantes aceros de herramientas ofrecen una resistencia a la descarburación buena.
- Clasificacion:
-Aceros al carbono: para la fabricación de herramientas para los usos más diversos, se emplean aceros sin elementos de aleación con porcentajes de carbono variables de 0.50 a 1.40%. para herramientas que deban tener gran tenacidad como martillos y picas; se emplean medios contenidos en carbono 0.50 a 0.70%. para herramientas de corte como brocas, cuchillas, y limas; calidades intermedias de 0.70 a 1%. Para conseguir en cada caso la máxima dureza, deben ser templados en agua.-Aceros rápidos: la característica fundamental de estos aceros es conservar su filo en caliente, pudiéndose trabajar con las herramientas casi a l rojo (600º) sin disminuir su rendimiento. Algunas composiciones típicas de los aceros rápidos son: C = 0.75%, W = 18%, Cr = 4% y V = 1% ; otra C = 0.75%, W = 18%, Co = 4% y V = 1.25%.-Aceros indeformables: reciben este nombre los aceros que en el temple no sufren casi deformaciones y con frecuencia después del temple y revenido quedan con dimensiones prácticamente idénticas a las que tenían antes del tratamiento. Esto se consigue empleando principalmente el cromo y el manganeso como elementos de aleación. Estos aceros templan con un simple enfriamiento al aire o en aceite. Composiciones típicas: C = 2% y Cr = 12%; C = 1% y Cr = 5% y otra C = 1% y Mn = 1%.-Aceros al corte no rápidos: se agrupan varios aceros aleados, principalmente con cromo y wolframio, muy empleados para la fabricación de herramientas de corte que no deben trabajar en condiciones muy forzadas. Pueden considerarse como unas calidades intermedias entre los aceros rápidos y los aceros al carbono, y la mayoría de herramientas fabricadas con ellos suelen quedar con durezas comprendidas entre 60 y 66 Rockwell-C.
ACEROS DE CEMENTACION
La cementación es un tratamiento termoquímico en el que se aporta carbono a la superficie de una pieza de acero mediante difusión, modificando su composición, impregnando la superficie hasta una profundidad adecuada y sometiéndola a continuación a un tratamiento térmico.Según sean los requisitos de dureza y resistencia mecánica existen varios tipos de aceros adecuados para recibir el tratamiento de cementación y posterior tratamiento térmico.
- Caracterisiticas de la cementacion:
-Endurece la superficie-No le afecta al corazón de la pieza-Aumenta el carbono de la superficie-Su temperatura de calentamiento es alrededor de los 900 ºC-Se rocía la superficie con polvos de cementar ( Productos cementantes)-El enfriamiento es lento y se hace necesario un tratamiento termico posterior-Los engranajes suelen ser piezas que se cementan
- Propiedades:
- Tenaz y maleable.
-Dureza.
-Resistencia al desgaste.
-Resistencia a la fatiga.
- Clasificacion:
Aceros para cementación al carbono: Cementación 900º-950º, primer temple 880º-910º en agua o aceite, segundo temple 740º-770º en agua. Revenido 200º máx.Aplicaciones: Piezas poco cargadas y de espesor reducido, de poca responsabilidad y escasa tenacidad en el núcleo.Aceros para cementación al Cr-Ni de 125kgf/mm2: Tiene en su composición un 1% de Cr y un 4,15% de Ni. Cementación 850º-900º, primer temple 900º-830º en aceite, segundo temple 740º-780º en aceite. Revenido 200º máx.Aplicaciones: Piezas de gran resistencia en el núcleo y buena tenacidad. Elementos de máquinas y motores. Engranajes, levas etc.Aceros para cementación al Cr-Mo de 95 kgf/mm2: Tiene en su composición un 1,15% de Cr y un 0,20% de Mo. Cementación 890º-940º; primer temple 870º-900º en aceite, segundo temple 790º-820º en aceite. Revenido 200º máx.Aplicaciones: Piezas para automóviles y maquinaria de gran dureza superficial y núcleo resistente. Piezas que sufran gran desgaste y transmitan esfuerzos elevados. Engranajes, levas, etc.Aceros para cementación al Cr-Ni-Mo de 135 kgf/mm2: Tiene en su composición un 0,65% de Cr, 4% de Ni y 0,25% de Mo. Cementación 880º-930º; primer temple 830º-860º aire o aceite;segundo temple 740º-770º aceite. Revenido 200º máx. Aplicaciones: Piezas de grandes dimensiones de alta resistencia y dureza superficial. Máquinas y motores de máxima responsabilidad., ruedas dentadas, etc.
ACERO PARA NITRURACION
La nitruración es un tratamiento termoquímico, que modifica la composición superficial del acero incorporando nitrógeno, dentro del proceso de tratamiento térmico.El objetivo principal de la nitruración iónica es mejorar las propiedades superficiales de piezas para maquinaria, herramientas y matrices, obteniendo una mayor dureza superficial, resistencia al desgaste, fatiga y corrosiónDicho proceso es aplicable con total eficiencia en aceros, fundiciones, materiales sinterizados y aceros inoxidablesEl tratamiento se realiza en vacío y bajo el efecto de un campo eléctrico, las moléculas de nitrógeno se disocian. A causa de una diferencia de potencial (300-1000 V), los iones positivos son lanzados sobre el cátodo constituido por las piezas a tratar, sobre las que se provoca un calentamiento por transformación de energía cinética de los iones, defectos en la red, pulverización de átomos en la superficie y una limpieza superficial lo que favorece la reactividad fisicoquímica necesaria para la formación de nitruros metálicos en la capa superficial.
- Caracteristicas:
-Endurece la superficie de la pieza-Aumenta el volumen de la pieza-Se emplean vapores de amoniaco-Es un tratamiento muy lento-Las piezas no requieren ningún otro tratamiento.
- Propiedades:
- Alta resistencia al desgaste por adhesion.
- Dureza de superficie alta.
- Reduccion de los coeficientes de friccion.
- Mejor resistencia a la corrosion.
- Resistencia a altas temperaturas.
- Resistencia a la fatiga.
- Resistencia a la abrasion.
- Clasificacion:
Acero para nitruración al Cr-Mo-V de alta resistencia: La composición extra de este acero es la siguiente: 0,32% C, 3,25% Cr, 0,40% Mo y 0,22%V. Una vez tratado alcanza una resistencia mecánica de 120 kg/mm2. La capa nitrurada se adhiere muy bien al núcleo sin temor a descascarillamiento. Se utiliza para construir piezas de gran resistencia y elevada dureza superficial para resistir el desgaste.Acero para nitruración al Cr-Mo-V de resistencia media: la composición extra de este acero es 0,25% C, 3,25%Cr, 0,40% Mo y 0,25% Mo. Tiene características y aplicaciones parecidos al anterior, solamente que su resistencia mecánica es de 100kg/mm2.Acero para nitruración al Cr-Al-Mo de alta dureza: la composición extra de este acero es 0,40% C, 1,50% Cr, 0,20% Mo y 1% Al. La capa nitrurada de este acero puede descascarillarse y es de gran fragilidad. Se utiliza para piezas que soporten una resistencia media y la mayor dureza superficial posible.
ACEROS INOXIDABLES
Los Aceros Inoxidables son una gama de aleaciones que contienen un mínimo de 11% de Cromo. El Cromo forma en la superficie del acero una película pasivante, extremadamente delgada, continua y estable. Esta película deja la superficie inerte a las reacciones químicas. Esta es la característica principal de resistencia a la corrosión de los aceros inoxidables.El extenso rango de propiedades y características secundarias, presentes en los aceros inoxidables hacen de ellos un grupo de aceros muy versátiles.La selección de los aceros inoxidables puede realizarse de acuerdo con sus características:· Resistencia a la corrosión y a la oxidación a temperaturas elevadas. · Propiedades mecánicas del acerol · Características de los procesos de transformación a que será sometido. · Costo total (reposición y mantenimiento).
- Propiedades: Los aceros inoxidables tienen una resistencia a la corrosión natural que se forma automáticamente, es decir no se adiciona. Tienen una gran resistencia mecánica, de al menos dos veces la del acero al carbono, son resistentes a temperaturas elevadas y a temperaturas criógenicas. Son fáciles de transformar en gran variedad de productos y tiene una apariencia estética, que puede variarse sometiendo el acero l a diferentes tratamientos superficiales para obtener acabado a espejo, satinado, coloreado, texturizado, etc.
ENSAYOS DE TALLER
Se denomina ensayo no destructivo (también llamado END, o en inglés NDT de nondestructive testing) a cualquier tipo de prueba practicada a un material que no altere de forma permanente sus propiedades físicas, químicas, mecánicas o dimensionales. Los ensayos no destructivos implican un daño imperceptible o nulo. Los diferentes métodos de ensayos no destructivos se basan en la aplicación de fenómenos físicos tales como ondas electromagnéticas, acústicas, elásticas, emisión de partículas subatómicas, capilaridad, absorción y cualquier tipo de prueba que no implique un daño considerable a la muestra examinada.
En general los ensayos no destructivos proveen datos menos exactos acerca del estado de la variable a medir que los ensayos destructivos. Sin embargo, suelen ser más baratos para el propietario de la pieza a examinar, ya que no implican la destrucción de la misma. En ocasiones los ensayos no destructivos buscan únicamente verificar la homogeneidad y continuidad del material analizado, por lo que se complementan con los datos provenientes de los ensayos destructivos.
La amplia aplicación de los métodos de ensayos no destructivos en materiales se encuentra resumida en los tres grupos siguientes:
Defectología. Permite la detección de discontinuidades, evaluación de la corrosión y deterioro por agentes ambientales; determinación de tensiones; detección de fugas.
Caracterización. Evaluación de las características químicas, estructurales, mecánicas y tecnológicas de los materiales; propiedades físicas (elásticas, eléctricas y electromagnéticas); transferencias de calor y trazado de isotermas.
Metrología. Control de espesores; medidas de espesores por un solo lado, medidas de espesores de recubrimiento; niveles de llenado.
RAYOS X
Una radiografía es una imagen registrada en una placa o película fotográfica. La imagen se obtiene al exponer dicha placa o película a una fuente de radiación de alta energía, comúnmente rayos X o radiación gamma procedente de isótopos radiactivos (Iridio 192, Cobalto 60, Cesio 137, etc.). Al interponer un objeto entre la fuente de radiación y la placa o película las partes más densas aparecen con un tono más o menos gris en función inversa a la densidad del objeto. Por ejemplo: si la radiación incide directamente sobre la placa o película, se registra un tono negro. Sus usos pueden ser tanto médicos, para detectar fisuras en huesos, como industriales en la detección de defectos en materiales y soldaduras tales como grietas, poros, "rechupes", etc.
Radiografía industrial
La radiografía industrial de molgilner ensayo no destructivo de tipo físico,que es utilizado para inspeccionar materiales en busca de discontinuidades macroscópicas y variaciones en su estructura interna. La radiación electromagnética de onda corta tiene la propiedad de poder penetrar diversos materiales sólidos, por lo que al utilizarla se puede generar una imagen de la estructura interna del material examinado. El principio de esta técnica consiste en que cuando la energía de los rayos X o gamma atraviesa una pieza, sufre una atenuación que es proporcional al espesor, densidad y estructura del material inspeccionado. Posteriormente, la energía que logra atravesar el material es registrada utilizando una placa fotosensible, de la cual se obtiene una imagen del área en estudio. los rayos x son una forma electromagnética(como una luz)que contiene una gran energía y por ello, es posible que penetre en el cuerpo humano, produciendo así, una imagen en una placa de fotografía. Durante este paso, las radiaciones se modifican, entonces, al pasar por estructuras de gran densidad como el hueso, la imagen que se producira en la placa será de color blanco y si atraviesa estructuras con aire se formara una imagen de color negro. Los colores dependerán de la densidad de las estructuras.
INSPECCION POR ULTRASONIDO
La inspección por ultrasonido se define como un procedimiento de inspección no destructivo de tipo mecánico, y su funcionamiento se basa en la impedancia acústica, la que se manifiesta como el producto de la velocidad máxima de propagación del sonido y la densidad del material. Cuando se inventó este procedimiento, se medía la disminución de intensidad de energía acústica cuando se hacían viajar ondas supersónicas en un material, requiriéndose el empleo de un emisor y un receptor. Actualmente se utiliza un único aparato que funciona como emisor y receptor, basándose en la propiedad característica del sonido de reflejarse al alcanzar una interfase acústica.
Los equipos de ultrasonido que se utilizan actualmente permiten detectar discontinuidades superficiales, su superficiales e internas, dependiendo del tipo de palpador utilizado y de las frecuencias que se seleccionen dentro de un rango que va desde 0.25 hasta 25 MHz. Las ondas ultrasónicas son generadas por un cristal o un cerámico piezoeléctrico denominado transductor y que tiene la propiedad de transformar la energía eléctrica en energía mecánica y viceversa. Al ser excitado eléctricamente el transductor vibra a altas frecuencias generando ultrasonido. Las vibraciones generadas son recibidas por el material que se va a inspeccionar, y durante el trayecto la intensidad de la energía sónica se atenúa exponencialmente con la distancia del recorrido. Al alcanzar la frontera del material, el haz sónico es reflejado, y se recibe el eco por otro (o el mismo) transductor. Su señal es filtrada e incrementada para ser enviada a un osciloscopio de rayos catódicos.
TINTAS PENETRANTES
La inspección por tintas penetrantes es un tipo de ensayo no destructivo que se utiliza para detectar e identificar discontinuidades presentes en la superficie de los materiales examinados. Generalmente se emplea en aleaciones no ferrosas, aunque también se puede utilizar para la inspección de materiales ferrosos cuando la inspección por partículas magnéticas es difícil de aplicar. En algunos casos se puede utilizar en materiales no metálicos. El procedimiento consiste en aplicar un líquido coloreado o fluorescente a la superficie en estudio, el cual penetra en cualquier discontinuidad que pudiera existir debido al fenómeno de capilaridad. Después de un determinado tiempo se remueve el exceso de líquido y se aplica un revelador, el cual absorbe el líquido que ha penetrado en las discontinuidades y sobre la capa del revelador se delinea el contorno de éstas.
Las aplicaciones de esta técnica son amplias, y van dese la inspección de piezas críticas como son los componentes aeronáuticos hasta los cerámicos como las vajillas de uso doméstico. Se pueden inspeccionar materiales metálicos, cerámicos vidriados, plásticos, porcelanas, recubrimientos electroquímicos, entre otros. Una de las desventajas que presenta este método es que sólo es aplicable a defectos superficiales y a materiales no porosos.
PARTICULAS MAGNETICAS
La inspección por partículas magnéticas es una tipo de ensayo no destructivo que permite detectar discontinuidades superficiales y su superficiales en materiales ferro magnéticos
El principio de este método consiste en que cuando se induce un campo magnético en un material ferro magnético, se forman distorsiones en este campo si el material presenta una zona en la que existen discontinuidades perpendiculares a las líneas del campo magnético, por lo que éstas se deforman o se producen polos. Estas distorsiones o polos atraen a las partículas magnéticas que son aplicadas en forma de polvo o suspensión en la superficie a examinar y por acumulación producen las indicaciones que se observan visualmente de forma directa o empleando luz ultravioleta. Sin embargo los defectos que son paralelos a las líneas del campo magnético no se aprecian, puesto que apenas distorsionan las líneas del campo magnético.
Se utiliza cuando se requiere una inspección más rápida que la que se logra empleando líquidos penetrantes. Existen 32 variantes del método, y cada una sirve para diferentes aplicaciones y niveles de sensibilidad.
Este método se utiliza en materiales ferro magnéticos como el hierro, el cobalto y el níquel. Debido a su baja permeabilidad magnética, no se aplica ni en los materiales paramagnéticos (como el aluminio, el titanio o el platino) ni en los diamagnéticos (como el cobre, la plata, el estaño o el zinc).
Los defectos que se pueden detectar son únicamente aquellos que están en la superficie o a poca profundidad. Cuanto menor sea el tamaño del defecto, menor será la profundidad a la que podrá ser detectado.
El campo magnético se puede generar mediante un imán permanente, un electroimán, una bobina o la circulación de intensidad eléctrica sobre la pieza. El imán permanente se suele utilizar poco debido a que solamente se pueden conseguir con él campos magnéticos débiles.
En una pieza alargada, la magnetización mediante bobina genera un campo magnético longitudinal, por lo que muestra defectos transversales. En cambio, una corriente eléctrica entre los extremos de la pieza genera un campo transversal, por lo que detecta defectos longitudinales.
ENSAYO DE CUÑA
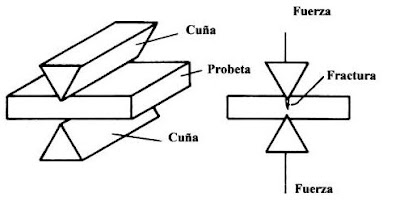
. Ensayo de compresión entre cuñas. Representación esquemática de: (a) las herramientas de ensayo y de la probeta; (b) Fractura de la probeta
En el ensayo de compresión entre cuñas una probeta es comprimida bajo la acción de una fuerza mono tónica hasta su ruptura, entre dos cuñas dispuestas en oposición y con sus planos de filos coincidentes (Figura 1). Una cuña es solidaria a la base del dispositivo de ensayo y la otra, sobre la que se aplica la fuerza, desliza sobre guías practicadas en el cuerpo del dispositivo. La mayoría de las especificaciones de ensayo coinciden en utilizar cuñas de acero templado y revenido para durezas de (62±2) Rockwell C con ángulo de filo de (90,0±0,5) grados. El radio de filo es menor que 0,2 mm, cuando se utiliza la probeta plana. La resistencia entre cuñas sc, se define como el cociente entre la máxima fuerza Fc, aplicada sobre las cuñas hasta la ruptura y el área transversal nominal inicial de la probeta Ac, localizada entre los filos de las cuñas:
sc= Fc/Ac (1)
La rapidez de confección de las probetas (planas) y de la realización del ensayo, posibilitan la utilización de la compresión entre cuñas como un método de control de calidad en la línea de producción. Si las probetas fueren retiradas de los canales de alimentación o de material adicionado mediante el uso de modelos superpuestos al de la pieza, el control de la calidad se torna no destructivo. En ambos casos el espesor del canal de alimentación o del material adicionado tiene que ser tal que la velocidad de enfriamiento durante la solidificación sea semejante a la de las paredes de las piezas, para conseguir la semejanza en sus propiedades mecánicas [1].
ENSAYO DE COLABILIDAD
Evidentemente no todos los materiales y sus aleaciones no tienen la misma viabilidad para su uso en la obtención de piezas fundidas, puesto que unos llenan completamente los moldes con mayor facilidad que otros.
A esta facilidad de llenar los moldes estando el metal en estado liquido se llama colabilidad. Esta propiedad depende de una serie de condiciones entre ella.
a. la deferencias entre la temperatura de colada y
b. y la solidificación del metal
Por tanto es mas elevada la colabilidad entre mayor sea la diferencia de temperatura
Sin embargo la temperatura de colada viene limitada a
por la capacidad del calentamiento de los hornos en unos casos
por las variaciones que puedan sufrir el metal fundido cuando la temperatura que se eleve pueda ser excesiva
La colabilidad es muy variable para algunos metales a otros para su medición, se ha establecido varios métodos
El mas utilizado universalmente consiste en colar las muestras del metal o aleación cuya colabilidad se desee determinar en un molde en forma de espiral de seccion triangular. La colabilidad se determinaba por la longitud de la espiral que el metal llega a llenar
ENSAYOS DEL TALLER
Determinación del estado de integridad general de una parte o componente, incluyendo la detección de grietas, desgaste, corrosión, erosión o cualquier daño físico en sus superficies.Detección de fugas de los componentes que retienen presión y posible camino de la fuga que pueda afectar a la integridad o correcta operabilidad del mismo y de otros componentes.
FABRICACION DE PROBETAS
Las probetas para examinar al microscopio son cortadas con una sierra o con otro medio adecuado, cuidando que durante tal operación no se recalientan.
Se alisa en seguida una cara con la lima y se pulimenta con tela de esmeril comenzando con una de grano grueso para acabar con la 1F, la 0, la 00, hasta la 000000 para probetas muy delicadas.
El pulimento se puede hacer a mano o con una pulimentadora.
Cuando se acaba con una tela es preciso tener cuidado que se hayan desaparecido las raya de la tela precedente. Siempre se procede cruzando la dirección del pulimento.
Después de ser pulimentada con la tela del esmeril, se bruñe la probeta.
Las probetas muy pequeñas pueden ser incrustada en una matriz de lacre, aleación de Wood o resina sintética, a fin de poder manejarla.
La pulimentadora consiste en un disco rotatorio (800-900 v/min) recubierto de fieltro, en el que se aplica el material abrasivo, o de oxido de hierro y de cromo, según el metal que hay que pulimentar
El matraz o frasco de Erlenmeyer (generalmente llamado sólo Erlenmeyer) es uno de los frascos de vidrio más ampliamente utilizados en laboratorios de química.
Descripción:
Consiste en un frasco cónico de vidrio de base ancha y cuello estrecho. Se los encuentra de diversas capacidades y con algunas variaciones. Suelen incluir unas pocas marcas para saber aproximadamente el volumen contenido. Fue creado en el año 1861 por Richard August Carl Emil Erlenmeyer (1825-1909).
Técnicas en las que se lo emplea
Gracias a la característica forma troncocónica del matraz se evita en gran medida la pérdida del líquido por agitación o por evaporación. También es importante que al disponer de un cuello estrecho es posible taparlo con un tapón esmerilado, o con algodón hidrófobo.
Es empleado en lugar del clásico vaso de precipitados cuando contienen un medio líquido que debe ser agitado constantemente (como en el caso de las titulaciones) sin riesgo de que se derrame su contenido, o cuando se debe trabajar con reacciones químicas violentas. Suele utilizarse para calentar sustancias a temperaturas altas aunque no vigorosamente; la segunda tarea suele dejársele al balón de destilación.
Otros usos:
En microbiología se lo emplea para la preparación de caldos de cultivo, entre otros motivos, por poder taparse fácilmente con un tapón de algodón hidrófobo.
Metodología de uso
Como todo material de vidrio tiene un método específico para utilizarlo correctamente. Para anclarlo, se puede colocar un peso de plomo o metal sobre el exterior.
Al calentarlo, suele colocarse sobre de alguna de las siguientes formas. Cuando se arma el aparato de estas maneras, suele colocarse una tela metálica entre el matraz y el aro o el trípode.
Sobre un trípode.
En un anillo o aro de metal que, a su vez, está aferrado a un soporte universal por medio de una doble nuez o algún asa similar. El aro lo mantiene sobre un mechero Bunsen para que la llama del mechero lo caliente.
Puede aferrarse el matraz directamente al soporte universal sosteniéndolo con una agarradera para tubos de ensayo en el cuello del matraz.
El matraz o frasco de Erlenmeyer (generalmente llamado sólo Erlenmeyer) es uno de los frascos de vidrio más ampliamente utilizados en laboratorios de química.
Descripción
Consiste en un frasco cónico de vidrio de base ancha y cuello estrecho. Se los encuentra de diversas capacidades y con algunas variaciones. Suelen incluir unas pocas marcas para saber aproximadamente el volumen contenido. Fue creado en el año 1861 por Richard August Carl Emil Erlenmeyer (1825-1909).
Técnicas en las que se lo emplea
Gracias a la característica forma troncocónica del matraz se evita en gran medida la pérdida del líquido por agitación o por evaporación. También es importante que al disponer de un cuello estrecho es posible taparlo con un tapón esmerilado, o con algodón hidrófobo.
Es empleado en lugar del clásico vaso de precipitados cuando contienen un medio líquido que debe ser agitado constantemente (como en el caso de las titulaciones) sin riesgo de que se derrame su contenido, o cuando se debe trabajar con reacciones químicas violentas. Suele utilizarse para calentar sustancias a temperaturas altas aunque no vigorosamente; la segunda tarea suele dejársele al balón de destilación.
Otros usos:
En microbiología se lo emplea para la preparación de caldos de cultivo, entre otros motivos, por poder taparse fácilmente con un tapón de algodón hidrófobo.
Metodología de uso
Como todo material de vidrio tiene un método específico para utilizarlo correctamente. Para anclarlo, se puede colocar un peso de plomo o metal sobre el exterior.
Al calentarlo, suele colocarse sobre de alguna de las siguientes formas. Cuando se arma el aparato de estas maneras, suele colocarse una tela metálica entre el matraz y el aro o el trípode.
Sobre un trípode.
En un anillo o aro de metal que, a su vez, está aferrado a un soporte universal por medio de una doble nuez o algún asa similar. El aro lo mantiene sobre un mechero Bunsen para que la llama del mechero lo caliente.
Puede aferrarse el matraz directamente al soporte universal sosteniéndolo con una agarradera para tubos de ensayo en el cuello del matraz.



Asegúrese que la pipeta Beral que use esté seca o endulzada con el agente valorante, así no se cambiará la concentración de la solución.
Anterior a la titulación, endulce la bureta con solución del agente valorante y verifique que la solución fluye libremente. Para endulzar un elemento de cristalería, lo debe enjuagar de manera que se cubra toda su superficie con la solución, entonces proceda al desagüe.
Endulzar dos o tres vez asegurará que la concentración del agente valorante no cambie por una gota residual de agua.
BURETA


Metodología de uso
Como todo material debe estar limpio antes de ser utilizado y es importante, mientras esté siendo usado con un reactivo o muestra, dejarlo en el recipiente (o, si este es demasiado pequeño, a su lado) para evitar confundirlo con otro. Además, al ser un material volumétrico no se lo debe someter a cambios bruscos ni a altas temperaturas.
Se introduce la pipeta (con la punta cónica para abajo) en el recipiente del cual se desea extraer un volumen determinado de muestra.
Se coloca la propipeta o una perita en la punta libre y se hace ascender el líquido por encima del aforo superior. NUNCA PIPETEAR CON LA BOCA.
Rápidamente se gradúa con la propipeta o se saca la perita colocando el dedo índice obturando la punta, para evitar que descienda.
Se disminuye leve y lentamente la presión ejercida por el dedo, hasta que el líquido comience a descender. Se vuelve a presionar cuando el menisco del líquido llegó a 0. Si el líquido descendió demasiado, se comienza nuevamente.
Se traslada la pipeta al recipiente destino.
Se disminuye nuevamente la presión del dedo hasta llegar a la cantidad de mililitros necesarios.
En el caso de las pipetas graduadas, para vaciarla completamente se saca el dedo completamente y se deja caer. Pero no se debe forzar la caída de las últimas gotas, sino que éstas deben quedar en la punta cónica de la pipeta.
En la pipeta graduada se pueden medir distintos volumenes de liquido, ya que lleva a una escala graduada.
La pipeta de vertido posee un unico enlace superior por lo que sólo puede medir un volúmen

El colorímetro permite la comparación de dos disoluciones, una de las cuales, para que pueda ser empleado con fines analíticos, debe ser de concentración conocida. Como puede observarse en la figura, la luz reflejada mediante el espejo inferior atraviesa los recipientes en los cuales se encuentran la muestra patrón y la muestra estudiada. Los tubos de vidrio (TC) permiten regular la distancia recorrida por el haz luminoso en la disolución. Finalmente, un prisma recoge estos rayos luminosos y los dirige al ocular, en el cual se pueden observar dos semicirculos procedentes cada uno de cada muestra y, de este modo, se puede comparar las intensidades de salida. Si se varía la posición de los tubos TC, que regulan el valor de la distancia recorrida por el rayo, se pueden obtener en el ocular dos semicirculos de igual intensidad y calcular el valor de la concentración de la disolución analizada, mediante el siguiente procedimiento:
I1 = Io * e-(k1c1d1) [1]
I2 = Io * e-(k2c2d2) [2]
Los valores d1 y d2 representan la longitud de las columnas de líquido que pueden regularse a voluntad, de modo que puede conseguirse que la intensidad final de la luz (I1) que atraviesa la disolución 1 sea igual a la intensidad final de la luz (I2) que atraviesa la disolución 2:
I1=I2
Igualando las ecuaciones [1] y [2] resulta: Io* e-(k1c1d1) = Io* e-(k2c2d2)
y simplificando la expresión queda: k1c1d1 = k2c2d2
Si las sustancias sometidas a análisis son las mismas, entonces los coeficiente de absorción molecular deben ser iguales , lo que permite simplificar la ecuación anterior y obtener un método para calcular la concentración de una disolución, si se conoce el valor de la otra:
c1 = c2 * d2/d1
Este tipo de instrumentos fueron reemplazados a partir de los años cuarenta de este siglo por los espectrofotómetros, que renovaron la popularidad de esta técnica. Estos instrumentos empleaban diversos métodos para la obtención de luz monocromática o, al menos, de un intervalo reducido de longitudes de onda, y la medida de la absorción se realizaba mediante células fotoeléctricas, las cuales habían comenzado a ser empleadas con tal fin desde principios de siglo por autores como Otto Berg y August H. Pfund. En la colección figura uno de los primeros modelos de colorímetro de estas características, diseñado por B. Lange, y procedente también de las Facultades de Ciencias. Consta de dos recipientes que sirven para introducir los prismas de cuarzo con la disolución analizada y una disolución de concentración conocida. Una célula fotoeléctrica permite medir la intensidad luminosa que atraviesa una y otra muestra, de modo que, si la concentración de una disolución es conocida puede calcularse la otra, mediante un procedimiento semejante al descrito en los párrafos anteriores. En este caso, las magnitudes que permanecen constantes son las distancias recorridas por los rayos luminosos y la magnitud calculada es la relación entre las intensidades de salida.
DESTILADOR DE AGUA
Ahora con la mejor tecnología de DESTILADO, este equipo esta diseñado para aquellas empresas que requieren de una calidad de agua excepcional, ya sea para agregarla a procesos o que requieren agua de esta calidad.el equipo maneja 650 galones por día, el equipo esta diseñado para ahorrar energía eléctrica contra la competencia. Produce agua de menos de 2 tds o ppm y se le puede agregar equipo de electro diálisis, cuando se requiere todavía menor TDS o PPM.Características Standard.Construida en acero inoxidable tipo 304 y 316 (bajo pedido).Fácil de instalar solo requiere conexión trifásica y tres conexiones de agua. Fácil de operar son sus sistemas de auto chequeo
PIPETA
La pipeta es un instrumento de laboratorio que permite medir alícuotas de líquido con bastante precisión. Suelen ser de vidrio. Está formado por un tubo transparente que termina en una de sus puntas de forma cónica, y tiene una graduación (una serie de marcas grabadas) indicando distintos volúmenes.
Algunas son graduadas o de simple aforo, es decir que se enrasa una vez en los cero mililitros, y luego se deja vaciar hasta el volumen que se necesite; mientras que otras, las denominadas de doble enrase o de doble aforo, se enrasa en la marca o aforo superior, se deja escurrir el líquido con precaución hasta enrasar en el aforo inferior(este tipo son consideradas volumétricas). Si bien poseen la desventaja de medir un volúmen fijo de líquido, las pipetas de doble aforo superan en gran medida a las graduadas en que su precisión es mucho mayor, ya que no se modifica el volumen medido si se les rompe o deforma la punta cónica.
Para realizar las succiones de líquido con mayor precisión, se utiliza, mas que nada en las pipetas de doble aforo, el dispositivo conocido como propipeta.
Dependiendo de su volumen, las pipetas tienen un límite de error.
ANALISIS QUIMICO
DETERMINACION DEL CARBONO: Se basa en la gran afinidad del carbono por el oxigeno, y consiste en combinar estos dos elementos a elevada temperatura, esto es, en provocar la combustión del carbono y formar CO2 según la conocida reacción C+ O2= CO2
DETERMINACION DEL SILICIO: Se basa en la transformación del si metálico en SiO2. Tratando la fundición con una mezcla oxidante del acido nítrico (HNO3) y sulfúrico (H2SO4) se obtiene el SiO2, que resulta sucesivamente insolubilizado. Siendo los nitratos y sulfatos de los otros elementos contenidos en la fundición solubles en agua o en los ácidos, la sílice insoluble se puede separar fácilmente.
DETERMINACION DEL MANGANESO: Todos los sistemas usados para la determinación del Mn se basan en la oxidación de este elemento con acido permanganico (HMnO4), y en sucesiva reducción de este ultimo por los sistemas normales del análisis manganometrico.
EL FOSFORO: Para ser dosado, es necesario transformarlo primero en acido fosforito con oxidante enérgicos. Precipitado con molibdato amonico, puede ser pesado, o como fosfomolibdato, o bien por sucesivo tratamiento de calcinación como pirofosfato de magnesio.
EL AZUFRE: Dos son los métodos para dosar el azufre, unos basado en la oxidación de este elemento con acido sulfúrico, que es luego precipitado y pesado como sulfato de bario, y el otro volumétrico, que consiste en la fijación del acido sulfhídrico, en una solución de acetato de cadmio y en una sucesiva titilación yodo métrica de este ultimo.
COLORIMETRO
El colorímetro es un aparato basado en la ley de absorción de la luz habitualmente conocida como de "Lambert-Beer". En realidad, estos dos autores nunca llegaron a colaborar puesto que un siglo separa el nacimiento de cada uno. Johann Heinrich Lambert (1728-1777) realizó sus principales contribuciones en el campo de la matemática y la física y publicó en 1760 un libro titulado Photometria, en el que señalaba la variación de la intensidad luminosa al atravesar un rayo de luz un número "m" de capas de cristal podía considerarse como una relación exponencial, con un valor característico ("n") para cada cristal. En 1852, August Beer (1825-1863) señaló que esta ley era aplicable a soluciones con diversa concentración y definió el coeficiente de absorción, con lo que sentó las bases de la fórmula que sigue siendo utilizada actualmente:
ln(I/Io) = -kcd donde
k= coeficiente de absorción molecular, característico de la sustancia absorbente para la luz de una determinada frecuencia. c= concentración molecular de la disolución d= espesor de la capa absorbente o distancia recorrida por el rayo luminoso
Esta propiedad comenzó a ser utilizada con fines analíticos gracias a los trabajos de Bunsen, Roscoe y Bahr, entre otros. El colorímetro más antiguo de la colección de la Universidad de Valencia es semejante al propuesto en 1870 por Jules Duboscq (1817-1886), un fabricante de instrumentos ópticos de París. Es un buen ejemplo de lo que Gaston Bacherlard denominaba “theorèmes réifiés” para hacer referencia a los instrumentos científicos. Dado que su forma y sus características muestran claramente las bases teóricas de su funcionamiento, este tipo de instrumentos resulta particularmente adecuados para ser empleados en la enseñanza, por ejemplo, en el estudio de las leyes de la colorimetría .
ENSAYOS FISICOS Y MECANICOS
Para este ensayo vale cuanto se ha dicho sobre el ensayo a al tracción, teniendo en cuenta que, en lugar de alargamiento, se hablara de acortamiento, y en vez de contracción, de engrosamiento.
ENSAYO A LA FLEXION: El en sayo a la flexión tiene normas fijas solo para el hierro colado. La flecha de la flexión se mide con nonius adecuado. La deformación sera en parte elástica y en parte permanente.
En la practica se lee la flecha de flexión en el limite de la deformación elástica (cuando, aun aumentando la carga, el dinamómetro no sube) y la carga maxima, para la cual vale la formula.
σf = 8 Ql
∏ d3
En la que
σf = carga unitaria convencional de rotura a la flexión
l= distancia en mm entre los apoyos
d= diámetro en mm
ENSAYO AL CORTE: Las fundiciones mecanicas comunes no teniendo alargamiento no son materiales tenaces; como tales no resultan adecuados para resistir los esfuerzos de tracción o de flexión, y las pruebas relativas no son confrontables con los datos resultantes de análogas pruebas efectuadas sobre otros metales o aleaciones.
ENSAYO A LA TORSION: La probeta se fija a dos mandíbulas, la anterior de las cuales, es giratoria por medio de un sistema de engraje de tornillo sin fin, la otra que lleva un péndulo, de brazo regulable, es arrastrada y origina el momento de torsión, cuyo valor se lee directamente sobre el cuadrante. Al mismo tiempo, el contrapeso traza un diagrama.
Las probetas son, en general, de longitud tal que resulte un trecho útil de 300 mm.
ENSAYO DE LA DUREZA: Los ensayos mas comunes (Brinell, Vickers, Rockwell) se basan en la resistencia a la penetración que opone la superficie del cuerpo en examen a una esfera durísima o a una punta de diamante que tratan de penetrar bajo una carga preestablecida.
Método brinell: Una esfera de acero templado de cojinetes de bolas, de diámetro determinado (10, 5, 2.5 mm) se hace penetrar, bajo una determinada carga estática y por un determinado tiempo (en general 30 seg.), en el material que se aprueba.
La dureza brinell es la relación entre la carga total Q en kilogramos y la superficie S en milímetros cuadrados de la huella (caquete esférico).
ENSAYO DE LA RESILENCIA: El ensayo de la resilencia es una prueba de de resistencia al choque y da una medida de la fragilidad de un material.
Según Charpa (a flexión sobre dos apoyos).- Se apoya contra dos sostenes una probeta entallada. De una determinada altura H se deja caer libremente un péndulo que lleva una cuchilla de percusión, la cual golpea la probeta, la rompe y prosigue su carrera hasta una cierta altura, que señala un indice
Según Izod (a flexión sobre muesca).- La barreta, que se empotra por un extremo, tiene tres entalladuras sobre tres caras ortogonales y saca la media de tres resultados de prueba.
ENSAYOS A LOS CHOQUES ALTERNOS: Para la fundición, en la que no se presta ensayo de resilencia, se usa a veces el ensayo a los choques alternos; la barreta es paralelepipedica, en bruto, con dimensiones de 40. 40. 200 mm, y se apoya sobre dos soportes de arista redondeada separados entre si 160 mm y fijados sobre un yunque de un peso al menos de 500 Kg. Dispuesto sobre una capa de arena; en el punto medio de la probeta se deja caer una masa redondeada, que al choque, desarrolla un trabajo L= P . h= 5 kgm.
ENSAYO DEL DESGASTE: Se entiende por desgaste perdida gradual de materia en la superficie de un cuerpo solidó producida involuntariamente por acciones mecanicas, particularmente por rozamiento.
Entre los varios tipos de desgaste se pueden distinguir los causados por:
Frotamiento por rodamiento con engrase
Frotamiento por rodamiento sin engrase.
Frotamiento por deslizamiento con engrase
Frotamiento por deslizamiento sin engrase.
Acción de materiales en polvo, líquidos con abrasivos (erosión) chorros violentos de agua (cavitación).
Objetivo practico de la prueba es el de confrontar la resistencia al desgaste de diversos materiales y con ello establecer una graduación de calidad para determinado empleo.
El resultado del método del ensayo, método que debe reproducir con aproximación suficiente las solicitaciones del caso practico.
DEFECTOLOGIA DE PIEZAS FUNDIDAS
CAUSAS: Cierre deficiente de la caja de moldeo o recarga insuficiente de la misma. Cajas defectuosas. Las placas modelo no son lo bastante rigidas o se hallan torcidas. Junta imperfecta.
SOLUCION: Vease la causa
EXUDACION: Burbuja de eutéctico en laa superficie de las piezas de aleación de aluminio fundidas en coquilla, exudadas durante elproceso de su tratamiento térmico.
CAUSAS: Recalentamiento accidental durante el tratamiento térmico. Concentracion o combinación de impurezas dentro de la composición se mantengan dentro de la composición especificada, resultando en un minimo punto de fusión eutéctico. Como causa coadyuvante puede señalarse un elevado contenido de gas.
SOLUCION: Es indudable que deberá evitarse el recalentamiento durante el tratamiento térmico. Procurarse que la composición se mantenga dentro de los limites especificados, pero aun asi pero se hace necesario limitar la temperatura 505°C. Habra que desgasificar el metal.
POROS DE GAS: Orificio esférico de variable tamaño y paredes brillantes, distribuidos con bastante uniformidad por toda sección de la pieza fundida. Los mayores suelen encontrarse en la sección mas espeza de la pieza por ser la ultima en solidificarse
CAUSAS: Gas en el metal
SOLUCION: Desgasifiquese el metal mediante su fusión en condiciones oxidantes, seguida de una dexosidacion regulada.
POROS POR ARENA: Cavidades irregulares que contienen arena.
CAUSAS: En determinados casos los poros de arena se resultas de una costra o abolladura, pero también pueden provenir de
· Rincones pronunciados y zonas débiles de arenas, en el bebedero
· Machos o moldes débiles por aglomerantes
· Deficiente ejecución del bebedero
· Trabajo poco esmerado
· Superficie tosca o insuficiente conocida en lo modelos
· Efecto del rebote directo del metal en fusión
SOLUCION: Las medidas a adoptar para la eliminación de este defecto se deducen de las causas mencionadas
RECHUPES: Cavidad ocasionada por la contracción liquida. Generalmente muy irregular y paredes rugorosas y de forma de depresión superficial del tamaño variable, denominándose entonces rechupe o embudo de colada.
CAUSAS: Diseño inapropiado de la pieza fundida, asi como inadecuados métodos de colada.
SOLUCION: Modifiquese el diseño para obtener secciones del metal mas uniformes y provéase mejor alimentación mediante la apropiada modificación de las coladas y maselotes.
INCLUSIONES DE OXIDO Y ESCORIA: Partes sucias en la superficie de caras mecanizadas.
CAUSAS: Descuido al escoriar y colar. Uso de cuchara sucia
SOLUCION: Escoriar y colar cuidadosamente para impedir que penetren en el molde escorias o cenizas
INCLUSIONES DE ESCORIA: Inclusiones no metalicas en la superficie de las piezas fundidas
CAUSAS: Metal fundido viscoso u oxidado
· Bebederos demasiados grandes
· No se limpia bien la caja
· Colada interrumpida
SOLUCION: Habra que asegurarse de que el metal esta caliente y conserva su fluides
· Reduzcase el area del canal de colada
· Introduzcanse colectores para la suciedad en el sistema de canalización de la colada.
· Mantengasen llenos los bebederos para que la suciedad y la escoria floten en el metal liquido
FALSA UNION FRIA: Falta de unión del metal en la confluencia de dos corrientes, dando lugar a que se produzcan aparentes grieta o a ruugas superficiales, asi como capaz de oxido
CAUSA: Fluidez insuficiente en el emetal
SOLUCION: Elevese la temperatura de colada o el tamaño y numero de los bebederos
APLASTAMIENTO: Desplazamiento de la arena en las portadas de machos o juntas de molde, lo que da lugar a que produzcan cavidades de forma regular o proyecciones de piezas fundidas
CAUSAS: Deficiente ejecución de las juntas de molde, dando origen a una presión excesiva y desigual en la superficie de la arena. Cajas de moldeo defectuosamente encajadas, o alabeadas
SOLUCION: Se deduce de lo expuesto
ALAVEO: Deformacion desarrollada en la pieza fundida entre la temperatura de solidificación y la temperatura ambiente
CAUSAS: Los modelos no han sido convenientemente curvados para que se adapten al diseño especial de la pieza que se trata de ejecutar.
SOLUCION: Convenientemente tolerancia de curvado en el modelo y procédase a modificar el diseño, si factible fuese, para facilitar el enfriamientouniforme de todas las partes.
GRIETAS DE CONTRACCION: Grieta producida al contraerse el metal durante su enfriamiento en el molde, o poco después de haber sido extraido de este. Las paredes de tales grietas se presentan a menudo descoloridas, según la temperatura de la pieza en el momento de producirse el fallo
CAUSAS: Los principales factores causantes de este defecto son el diseño, de la fundición, unido a la falta de libertad para desarrollarse la contracción normal del metal, a consecuencias de los refuerzos de la caja, el molde o los machos etc.
SOLUCION: Utilicese una arena mas débil para molde y el macho, procurando que los esfuerzos de la de moldeo no coarten la contracción
SOPLADURAS: Cavidades de forma redondeada y paredes lisas y brillantes. El origen de esta falla puede determinarse procediéndo a seccionar la pieza.
CAUSA: Excesiva generación de gas de la arena de moldeo o macho, asi como insuficiente permeabilidad o aires. E l metal penetra en los aires.
SOLUCION: Utilice con menos profusión el aglutinante de aceite. Procurar que los machos estén convenientemente secados. Se aumentara la permeabilidad de la arena y proveerá de suficientes aires el molde y los machos.
JUNTA DESPLAZADA: Pronunciado desencaje de las partes de superior e inferior del molde, dando lugar a que la pieza fundida sea defectuosa.
CAUSAS: Desgaste de la caja y placa de moldeo, que origina el desplazamiento de la caja.
SOLUCION: Las chavetas y espigas de la caja deberán ser repasadas y renovadas regularmente, en caso de desgaste.